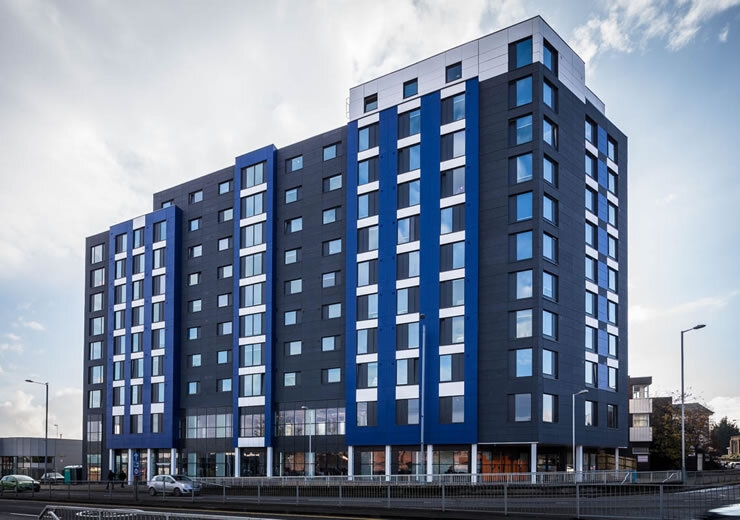
Product:
Durapipe HTA
Solution:
Speed of installation
Project:
Hatbox, University of Bedfordshire
Installer:
Thames Valley Mechanical
The Challenge
A new £12m student accommodation development, which has adopted an innovative pod design to achieve challenging build deadlines, has utilised Durapipe HTA pipework to help with the speed of installation.
The Solution
Hatbox, a new contemporary student accommodation complex in Luton operated by CRM Students, is a state-of-the art living experience for University of Bedfordshire students. Comprising 199 rooms, the 11 storey development offers 151 studio bedrooms with shower room and 35 en-suite bedrooms over the top nine floors, with a range of communal leisure facilities, a pharmacy and a doctor’s surgery occupying the ground and first floors.
With a strict timeframe for the build project to ensure it was complete for the start of term, developers turned to modular construction specialists Elements Europe to manufacture and install 199 room pods. The innovative construction method saw the pods constructed off-site in just 11 weeks and then installed on-site, within the steel frame structure, at a rate of 13 per day over a seven week period.
Using a modular construction technique significantly reduced build time and so developers needed to ensure all mechanical and electrical services to be installed on-site offered similar time-saving benefits. Thames Valley Mechanical was tasked with installing a hot and cold water system for the development and turned to Durapipe HTA for the pipework requirements.
Each pod needed connecting to the water mains on site and so Durapipe HTA in sizes up to 110mm was installed for the main service riser, which transfers water from the main storage tank in the basement plant room, via a pump set, up to the top floor plant room, which houses the boiler. This then feeds smaller risers to distribute the hot and cold water to each floor, which are all connected to the main pipe run and hot and cold returns on the first floor.
Thames Valley Mechanical had not previously used Durapipe HTA but selected the system for this project specifically due to its speed of installation, which aided the quick connection of the pods on site. As a new user of the system, Aliacis UK’s technical support team provided extensive assistance with on-site training for installers, as well as offering detailed advice regarding the quantity and positioning of expansion loops throughout the pipe network, in order to adequately compensate for expansion.
Commenting on the project, Rob Saunders, director of Thames Valley Mechanical, said: “With the time frame for this project being so strict, and delays just not an option, I needed a reliable pipe system that offered installation time savings. After visiting a similar project with an off-site pod design, which had utilised Durapipe HTA, I looked into the product. After considering a few options, Durapipe HTA looked to be the most effective product for this job, offering a reliable, high performance standard for the end user, while we benefitted from the reduced labour time that comes with its quick and easy jointing method. We found the installation process considerably quicker than alterative products we have used previously and so I will consider Durapipe HTA for future projects.”